Why continuously monitor a cleanroom?
Cleanroom monitoring is performed for two reasons:
- To certify the environment meets the specifications required by the FDA (ISO Classification), USP, BOH, and any other regulatory bodies. Cleanrooms must meet these standards and requirements to guarantee product safety. A cleanroom is an active environment with moving people, processes, and product. Contamination can happen at any time and negatively impacts both the yield and quality of the products manufactured inside the space. Without a continuous environmental monitoring system in place, these events can go undetected for days if not weeks, resulting in millions of dollars' worth of product flowing through a contaminated cleanroom and potentially a very expensive product discard or recall situation. Most users of a continuous environmental monitoring system see a full return on investment after the first few contamination event notifications.
- To record historical data which supports audits and internal standard operating procedures (SOPs). Historical data can be useful in many ways. Such information can be useful to determine maintenance and cleaning schedules, as well as be the records required by many regulatory agencies, customers, and internal data retention mandates.
Why not have people manually check each area?
That is what has been done historically, but taking one reading is not sufficient to fully understand how many particles are in the space at a given point or over time. And more importantly, manual recordings are very labor intensive and prone to human error.
In order to ensure the quality of the product being manufactured, particle counts should be taken in multiple places, especially where the product is exposed or the process produces shedding. A continuous environmental monitoring system will detect particle count spikes before they can cause issues, helping to avert a potentially disastrous and expensive contamination issue.
How to best monitor a cleanroom?
The first step to monitoring a cleanroom is to understand both the design of and risks for your cleanroom:
- Where are the most crucial, active, and dirty production areas that would be most impacted by contamination?
- Assess data from particle counters when cleanroom is in operation to better understand which locations are most at risk (or dirty)
- A continuous environmental monitoring system can track, record, and alarm in real-time when limits are reached
What size particles need to be monitored?
This depends on what is being produced and the ISO Class the cleanroom is looking to achieve. First, consider what size particles can impact production and classification level. Next, take into account budget and how best to position particle counters in the cleanroom. Keep in mind that particles can be a variety of sizes, so a particle counter that can monitor multiple particle sizes could be the most effective tool, like the Setra Particle Counter 5000 or 7000 series.
Where is the best place to sample particulate counts?
Again, this depends on what is being produced inside the cleanroom and the processes in place. In order to ensure the quality of the product being manufactured, particle counts should be taken in multiple places, especially where the product is exposed or the process produces shedding. Be mindful that taking particle count samples near filtered/clean air diffusers (HEPA/ULPA) can lead to readings not reflective of the actual particle readings at the product level or work surfaces.
Why not use a building automation system to monitor a cleanroom?
Technically, you can monitor a cleanroom with a building management or automation system (BMS/BAS). However, the main responsibility of these control systems is to help the facilities team keep the building running between a given set of control points. It is often challenging or not possible to get real-time environmental data from these systems for reporting purposes. While control of the building is critical to maintaining a safe environment, a continuous environmental monitoring system allows quality, engineering, or contamination control teams to meet regulatory requirements for data and reporting. It also supports real-time notifications of deviations in the environment to avoid costly contamination issues.
It is possible to integrate our continuous environmental monitoring system with a BMS/BAS. We support uni-directional integration of data from the continuous environmental monitoring system to the control system.
What's the difference between a building automation system and an environmental monitoring system?
A building automation system is designed to control the various parameters in a facility, adjusting immediately for the cleanroom being outside of its specifications. An environmental monitoring system is designed to gather, notify, and analyze more detailed cleanroom environmental data. Although there may be overlap between the two systems, they are distinctly different and both necessary for a state-of-the-art cleanroom.
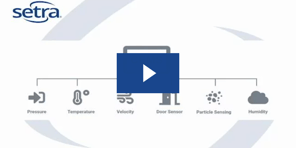
Looking to learn more about cleanroom environmental monitoring? Take a look at this video!